New technology speeds runway grading
Although reconstruction of the longest runway at the Mitchell, South Dakota Municipal Airport had fallen behind by about two weeks due to wet weather, Bowes Construction–the grading contractor–had two weapons to make up for lost time: a fast-track pavement recycling process and high-speed machine control technology.
A technique that is fairly unique to airport construction was used–demolishing and grading half of the runway at a time lengthwise–on the project, which received $6.7 million in funding under the American Recovery and Reinvestment Act of 2009. Once grading was complete, Commercial Asphalt, Mitchell, South Dakota, a division of Spencer Quarries, would reconstruct the runway with a 5½-inch-thick asphalt surface. Bowes Construction had equipped for the first time the second of two dozers–a Caterpillar D8T–with the Topcon 3D-MC² machine-control system for grading of the subbase and base. The company had already purchased 3D-MC² components from Laser Control Inc., Bloomington, MN and equipped the D6R with the system the previous May. The Topcon 3D-MC² system’s MC² sensor combines a gyro, compass and inertial sensor to measure the X, Y and Z position as well as the roll, pitch, yaw and acceleration of the dozer. The technology gives the system the capability to provide blade position readings up to 100 times per second–or roughly five times as many as alternative systems.
Additionally, testing indicates that the system yields about three times the grading smoothness of other machine-control systems. It can allow grading with twice the productivity of other systems, and four times the productivity of grading without the use of machine control.
Inside the dozer, operator LaDuke Palmer viewed the dozer’s position and blade placement in real time on the GX-60 in-cab monitor and made necessary adjustments. “When you use this system on a dozer, you’re really thinking like you’re operating a [grader],” he said. “You’re really knocking the big rows down so the blade can come in and finish-grade it.”
According to Jason Bowes, vice president of Bowes Construction, after cutting the subgrade excavation, Bowes Construction would check the grade as it was doing when using machine control. But “then you’d have a survey crew, which would be the engineer’s crew, staking it. And then, after it was staked, after the bluetops were put in, you’d have to grade the material over the stakes, so there would be another step. That’s probably the biggest difference with this system: scheduling our own work and continuing to move without being held up due to waiting for a staker to get in between each phase, which allows us to keep on moving.”
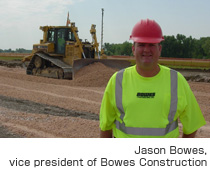
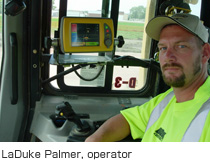
COMPANY:Bowes Construction